The Amp Dogs
- joepampel
- Jul 3, 2020
- 12 min read
Updated: May 19, 2022
Back in the days when Prodigy was the big alternate to AOL and the internet was a thing you tied up your POTS line to connect to, people with peculiar amp proclivities began to find each other. Like particles of dust settling on a microphone capsule... P* had groups (much like Facebook does) where you could create topics and others could join to discuss them. P* had a musicians group and under that group a fellow named Jim created a topic called "Amps n more" Jim was really into cool guitar tones and vintage gear. He was also a medical school administrator, competitive chili chef and (literally) worked on the Clinton health care plan, and finally, got me hooked on real BBQ. Phew! Eventually I would do repairs for him and wind up buying his '52 Fender Pro Amp and EP2 Echoplex. An expensive, but rewarding friendship. There were also some great Usenet groups, alt.guitar.amps, rec.audio.tubes and other groups. A lot of it is still out there. Take it with a grain of salt, we were all learning. (and we all still are)
Before long, a new member named Ted Weber joined the Prodigy group. I met Ted in a thread about Fender amps hanging their tubes upside down. Ted made some bright, well informed and cogent comments about it, ending up on it being a poor design choice. I took the other side; namely that these amps have toured the world for 50+ years and are the gold standard of reliability. As I recall it, he conceded that the evidence held that it was a successful design, despite what might seem at first to be ill advised. He was a powertrain engineer for GM, and I am a bit of a motor head. We had a lot more in common, and became good friends over time. There was a good sized regular group with some floaters and a steady stream of folks dropping out and folks joining. This was around the time I was learning which components made a big difference, and one thing that really seemed to be critical was speakers. They varied a great deal in not just efficiency (how much sound they made for a given input level) but also in frequency response, distortion characteristics, compression and more. I was having a hard time locating old "Fender style" speakers in good shape and the new ones with the exception of Naylor & Kendrick were mostly disappointing. Old speakers were scarce, expensive and fragile. No one seemed to be using AlNiCo magnets, and the ceramics just didn't feel right in some circuits.
Speakers haven't changed materially in about a century. There is a magnet that has a coil of wire suspended in it. This coil is wound around a circular former. The coil of wire is driven by an audio signal and that causes it to move towards and away from the magnet as the signal swings positively and negatively. The coil sits in a circular opening in the magnet. We attach a suspension (to locate the coil) and a cone (to match the impedance of the air, ideally) and that's about it. Coil moves, cone pushes air and we hear the signal. The efficiency of the speaker at a high level comes down to the amount of magnetism and the size of the gap. (there is a lot more, of course) Flux follows the inverse square law, so ideally you want a very powerful magnet and a very tight voice coil gap.
At first mfrs used a field coil; an electro-magnet that typically ran off the high voltage (or B+supply, named for the "B" batteries of old). They could be very powerful, but also heavy and complex, with exposed high voltage wiring. They owned the market through the 30's and 40's into the early 50's. AlNiCo was the first viable permanent magnet that could compete on strength and it was lighter and less expensive. It is an Iron alloy with Aluminum, Nickel and Cobalt as the primary other ingredients. (all magnets use Iron) AlNiCo ruled the market from about the early 50's until the early 60's when Ceramic magnets took over.
When Fender re-introduced the P10R (in the 1959 Bassman re-issue) they opted for a Kapton (hi temp plastic) voice coil former which altered the speaker's sound and opened the door for a company called Mojo Musical Supply to get their own version built with a proper paper former. As we noted above, the coil and former are held in place by a suspension, and changing the weight of the coil (and the thickness of it as well in this case) alters how the speaker responds. Mojo's were enormously popular, needless to say. And it really jammed the door open for a new generation of guitarists to have options.
Well, I talked to Ted about speakers and building amps a lot and the need for good old style ones. In time I learned that his brother in law was Kent Pyle, of the Pyle Company family. You might know Pyle speakers from thumping car audio, but back in the day I learned they were formerly known as Utah - and they contract manufactured speakers for Fender, Vox and others. One thing led to another and he got the crazy idea to try making some from our conversations. First for me, (I think that lasted maybe 5 minutes..) then a few certain models and then a bold plan to make a huge array of models out of the gate. I had nothing to do with the huge array, that was all Ted. I just wanted a few select, awesome reproductions. He wanted to conquer the world. Shock and Awe.
The marketing plan was simple; I borrowed Larry DiMarzio's in essence - my read of his is that Dimarzio sells pickups as point solutions to specific problems. They are inexpensive, easy to install and can make dramatic changes that are easy to hear by the end user. As the buyer, you hear the value right away. The idea launched a cottage industry of pickup manufacturers, but as far as I know, he was first. Thank you, Larry. Speakers to me are much the same; like pickups they are transducers (where electrons meet the air), both relatively quick and easy to install, both make a very audible difference, and both can solve for specific shortcomings in your guitar-amplifier system. As a tribute to his vision, and perhaps ours, there are now a raft of boutique speaker manufacturers with a wide array of models available for solving for specific problems. The best of all possible worlds really - having choices! It's hard to believe that at one time there weren't pages of different speaker models to choose from.
Well, eventually P* kicked us off, "these aren't musician discussions!" they scolded me. "We are musicians and this IS what we talk about" I responded. Tl;dr, we left P* and joined another dialup service, which was short lived before Ted informed us he was going to roll his own where we wouldn't have this issue ever again. It would be invite only, and we'd try and gather the most interesting folks we possibly could to exchange info and experience around old tube amps. The bunch of us informally referred to ourselves as 'amp dogs', I forget where that came from, but it stuck. Ted wrote an offline reader than ran in DOS, probably in Basic, but I don't know. He set up a phone line and an old PC at his house in Kokomo and over the next few weeks we all got a refresher course on our Hayes codes until everyone could log in. You would download all the new messages, reply on your end and then dial up again to upload your responses. Classic async communication. By the time we left P* there was a lot more interest in vintage amps, and more folks were taking the plunge to manufacture their own. A bunch were on P* with us and moved over to Teds Amps N More BBS. Some are household names today, some are just well known in the field. Mark Baier (Victoria Amp Co) and Mike Zaite (Dr. Z), are probably the two best known. Simcha Delft (my partner in OEI), Rick Erickson (Erickson Audio and former tech for Heart, Pearl Jam, Sound Garden, Neil Young, etc. Rick designed and built the custom flanger used to record "Barracuda" among other things!), Randall Aiken of Aiken Amps, "NY Dave" Dave Stork, Dave Funk, Fender custom shop legend (and co-inventor of 'relic-ing') Vince Cunetto, and many, many others were also on the BBS. In time many of us moved on from it and joined Tboy's perl coded masterpiece "Ampage". It's always been something nearly miraculous to find kindred souls with the same sorts of obscure interests. For me it's this really neat intersection of engineering, physics, music and black magic. The deeper you go, the more you find we don't understand or can't predict. You estimate, you guess, you theorize and debate but in the end all you can really do is listen and see how you did. Then you lick your wounds, rinse, repeat, lol. It's exciting. Speakers in particular have more than their share of magic. The magnetic motors have some quirks, the spider and surround that form the suspension do too, and of course the cone itself and dust cover. And then how it all goes together to form a system that has a range of behaviors that work with your guitar and amp to achieve a very complex result that is actually impossible to model. The digital systems I've gotten a look at all derive an aggregate function (input signal vs output signal) rather than try to model all of the intricacies of the real thing. The books I've read that dig deeply and mathematically into the basic circuits completely skip over the output transformer and speaker interface. It's that complex. 100 year old tech we still can't fully grasp. What can I say, I love that!
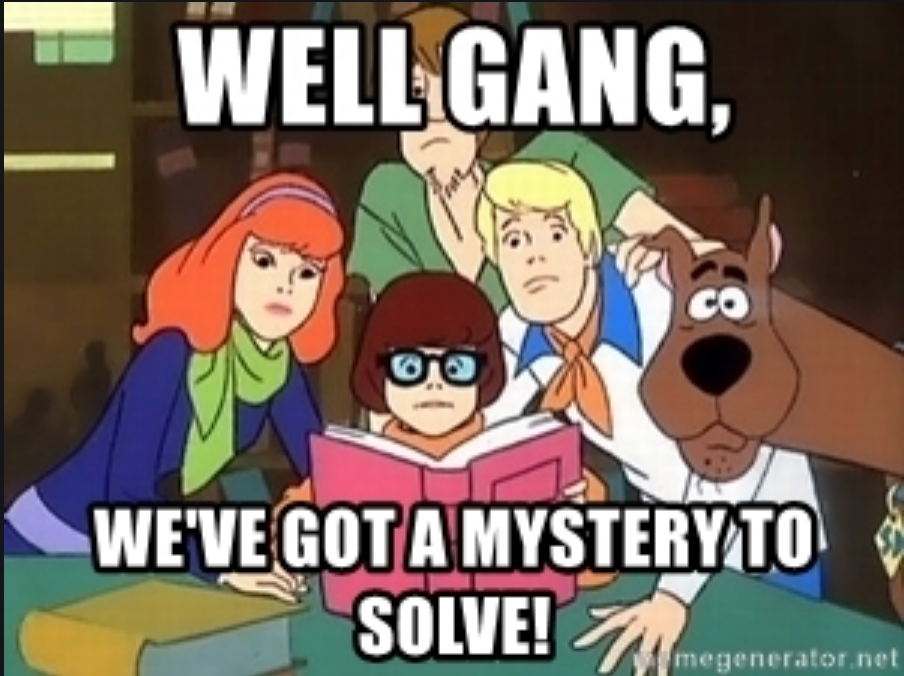
Ted and I schemed about speakers for days, weeks, months... To be clear, he did all the heavy lifting, finding suppliers, tooling, a place to supply blank baskets, putting up money and finding a building. I was busy going bankrupt at the garage (another blog, someday) He lucked out and found used tooling to punch the baskets; having that made would have been prohibitively expensive. (You take a blank bowl and punch out the windows in a press) Looking back, that might have been what put it all over the top.
I gave input on authenticity and sonic results; I did a lot of listening to and testing of prototypes. I had years of playing live and doing repairs behind me. Ted didn't play much guitar, although he could pick through "Walk Don't Run" better than he'd admit to. I also did a ton of public relations, answering inquiries, dealing with loudmouths that were trying to stop him before he started, the whole gamut.
I was pretty adamant we should get as close as possible in looks and performance and resist the urge to re-engineer them. That mostly held; Ted did make some changes to the motor design to streamline assembly and boost quality and he also changed paper coil formers out for Nomex to increase the power handling while not messing with the sprung weight and size of the cone assembly - or the tolerances of the magnetic motor. He was an engineer first, and he really wanted to re-engineer them! In the end he tightened up the tolerances a tiny bit which should make them more sensitive and efficient. (there was never any instrumented A/B testing I'm aware of) Magnetism varies by the square of the distance, so every little bit counts. My basic concerns centered around FUD - if you change stuff a) that customers expect to be there and b) that you haven't properly A/B tested, you now have an uphill battle to convince people your stuff is "the same" (or better) and you don't really know if it is. You've made problems where none existed, for no good reason. You've also left an opening for a competitor to attack you on it. "they didn't do the thing!" (regardless of whether the thing actually matters!) Far easier (but still hard) to build a repro/tribute speaker, call it a Silver bell and have it look kinda like a Celestion silver - making sure it sounds close is the hardest part. Same basket, magnet, cone details (material, seamed or molded, number of ribs, doping or no, etc.) right down to the tinsel wire & terminals. The cones are part of the "black art". Every manufacturer has their own witches brew of ingredients, some mix of wood pulp and other materials to get a specific weight to stiffness ratio. They are far from an "off the shelf" item, and it's not like all the same firms are in business making the same parts they did then. It's a lot of detective work and testing to find something usable. Back then a company like Fender would contract someone like Jensen to make speakers for them. Jensen would tweak prototypes for Fender to try, eventually settling on some mix of parts they liked. That mix would then get a Fender part # and not be sold to other clients. It's a good news/bad news thing. If you find a P12Q from an old Hammond organ, for instance, it will not be the same as a Fender-spec Jensen P12Q, but you can get it re-coned with the best modern replacement parts for a Fender-spec P12Q. The motor & basket don't change. Celestion are the kings of this; all of their 12" speakers use a 1.75" voice coil so they just play mix and match with the soft parts and magnet size to get a whole line of products.
If you get on the wayback machine, the earliest iterations of the Weber website feature reviews from me, and a thanks paragraph that starts with Jim, for starting that group on Prodigy (see below) that led to all this. Also Ted's idea. The company name was a compromise between the two of us. He really wanted his name on the company; I was concerned about him getting confused with the Mr Weber in Texas who made amps and had a tendency to sometimes say questionable things. Vintage Sound Technology shortened nicely to VST, and was of course open to all kinds of products. (as was his name to be fair). I was pushing for that. So in true Ted fashion, he decided to join them both.
Also in true Ted fashion, he (and I) researched the heck out of stuff. With so much guessing, heresay and old wives tales, there was a lot to cut through. Magnetic materials in particular (AlNiCo vs Ceramic) got a lot of scrutiny, and we did in fact find that AlNiCo acts differently than Ceramic magnets do, it's really pretty remarkable. It's also very expensive due to the Cobalt, and the conditions around how and where Cobalt is mined are terrible unfortunately.
Here is the very first version of the WeberVST web site. I'm pretty sure Ted wrote raw HTML in a text editor:
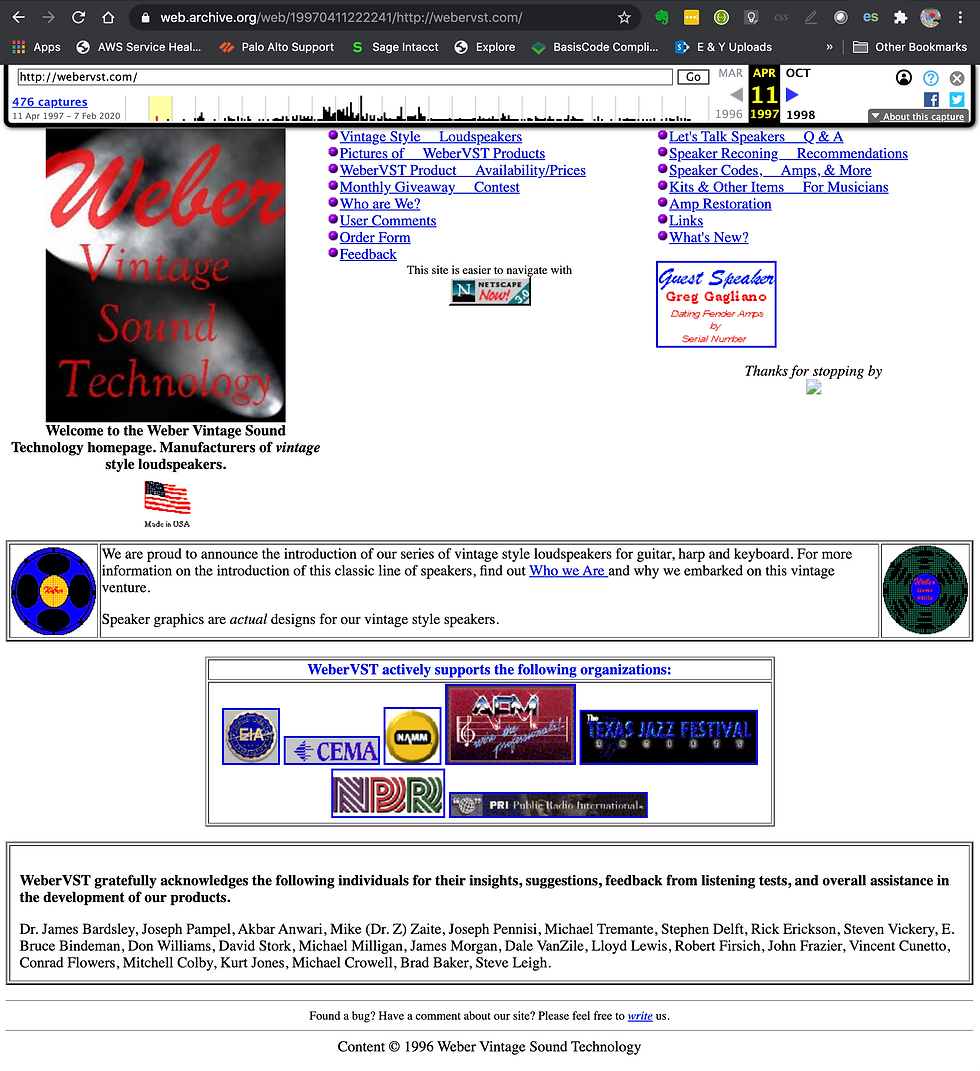
When VST launched as a company, Ted threw a party at a blues bar in Kokomo. NY Dave, myself and Akbar (both also in the thank you, above) carpooled it out there. We stopped in Ohio at Dr. Z's house on the way and had burgers with him. He was on the verge of setting up a real shop but was still in his basement with a garage full of head cabinets and a very patient Mrs Z was supporting his efforts. The kind of thing we all dreamed about. We made lots of noise in his basement and talked about all manner of tube nerd stuff. It was great.
We then drove out to Indy, stayed at Ted's house and went to the blues jam in Kokomo. Somewhere there is a video of it floating around, you know, in case I ever run for office.
Later, when Pyle was looking for someone to help run some of their operations (I forget exactly what the role was) Ted recommended me for an interview. I had a good chat with them, really nice folks. This would have been around summer 1997 I think. We'd recently bought a house though, I'd lived in the NYC area all my life and in fact my family has been in the area for 400 years now. Plus my wife was now teaching full time, and our primary responsible adult/breadwinner.. net net, I did not want to move to Indiana and start over, so that was that. Lucky thing too; within a year Pyle was bought out by Harmon. I would have moved there and lost my job, probably before Mrs P was even re-certified to teach in IN. Eek. Sometimes you're the windshield...
I took no compensation from Weber; I kept a few prototypes for years of effort. It was a lot of fun, and Ted was my friend. He taught me a lot. It's been very rewarding to see the company thrive and continue to this day with a good and well-earned reputation for quality and value.

Here's the back of Dave's head, playing his red Strat in Ted's basement. Ted had built one of every kind of cabinet to test speakers. If you haven't picked up on it yet, he chain smoked, had a caffeine IV running and didn't seem to sleep that much. He was always going. He spoke in schematics and FFT diagrams. We sometimes referred to him as the "Heat Miser" because he could tie just about any systemic constraint back to heat generation; it was pretty remarkable really. Anyhow, it was quite a scene there. The kind of weekend you might imagine it was, beers, a bunch of guys yakking and lots of guitar playing. Since it's my blog, that's my home-built tweed Super in front of the 2x15. The amp to the right of it is one of Dave's custom builds. The BF Bandmaster on the floor (left of the trunk) is one I had and fixed up and gave to Ted as a thank you for all his help. Way off to the left you can see the Tweed Deluxe Ted scored at the Indy Hamfest: with the original cover for $20! He must have been doing something right!

The crew: L-R Steve Vickery, Me, Mark Baier (Victoria Amp Co), Dave Stork, Ted, Akbar & Bruce Bindeman on kickoff weekend. "It Might Get Loud"
Comments