Fixing Our Stove
- joepampel
- Jan 19
- 11 min read
Updated: Jan 21
Our home came with a stove in it, like most homes do. It is a dual fuel 36" range with a gas cooktop and an electric oven. It is a DCS-RD366* on the very off chance that anyone else still has one. The house was built in 1997, 28 years ago. DCS, the mfr, does not even make stoves like this anymore. Needless to say parts for a stove this old can be a challenge to find, as can someone to service it. But new stoves can cost a lot of money; one this nice can easily run $5-10K plus installation. What do do? (where is my screwdriver?)
(* R for Range, D for dual fuel, 36" wide with 6 burners)
Safety First Note: Turn off the breakers for your stove before you do any work inside it. A 240V feed or even 120V - will kill you without breaking a sweat.
Learning basic electrical theory and how to read a schematic is a key life skill. I will probably write that a lot in this blog. You don't need to be an EE to fix stuff, you need a schematic and some very basic understanding of what is going on. For now, just chant "ohm's law" to yourself like a mantra. (V = I R, P = I * V)
Right before the holidays this year, our oven stopped getting hot. So armed with my trusty multimeter and an oversized helping of stubbornness, I started poking around, and I looked online at appliance repair forums to see what I could learn. At first I was looking for electrical info online and there wasn't anything that was the correct model, so I made some assumptions, like the diagrams I found were 'close enough' to get me started. In general they were.
The most common issues in my experience tend to happen where the most current or heat is dealt with. In most devices, that will be the power supply. In an electric oven the heating elements deal with a lot, going from room temp to 500F or more, over and over. Not surprisingly, the online 'fixit folks' were replacing them a lot and it's an easy thing to do - sometimes.
Our oven has 2 elements, one at the top for broiling and one at the bottom for baking. In practice, both get turned on when you bake in this oven. I turned the oven on, waited 5 minutes and then used my infra-red thermometer to check each coil. The broiler element was already 350 F, but the baking element was barely 100F - it was either dead or not getting power. I could not get to the contacts on the heating element, they were inside the back of the oven. If I had the right wiring diagram, I would have seen that both coils get power from the hotwire relay and I could have measured this right away. But I didn't, so I ordered a new baking element.
I found a replacement baking coil online and purchased it. Then I got to work pulling the old one out. A careless design made it a lot trickier than it ever should have been. So much for 'scandanavian design', they must have outsourced this one. There is a fan in the rear of the oven for convection baking, and the fan has a baffle in front of it to protect it from food spillage etc. That is all fine, but the baffle completely blocks the 2 phillips head screws you have to remove to get the old heating coil out. I tried all kinds of special tools, mirrors, etc. to get behind it (I am used to working on a 911 after all) but in the end had to remove it. And while that was just 4 screws, it was far more evil. Each screw was a long sheet metal screw and after it passed through the baffle there were 2 washers and then a long copper spacer tube. None of it held in place, and the lower left one could not be reached because the baffle had an extra bit in the way. Getting it out was not a problem, but getting it all back in would be a real pain.
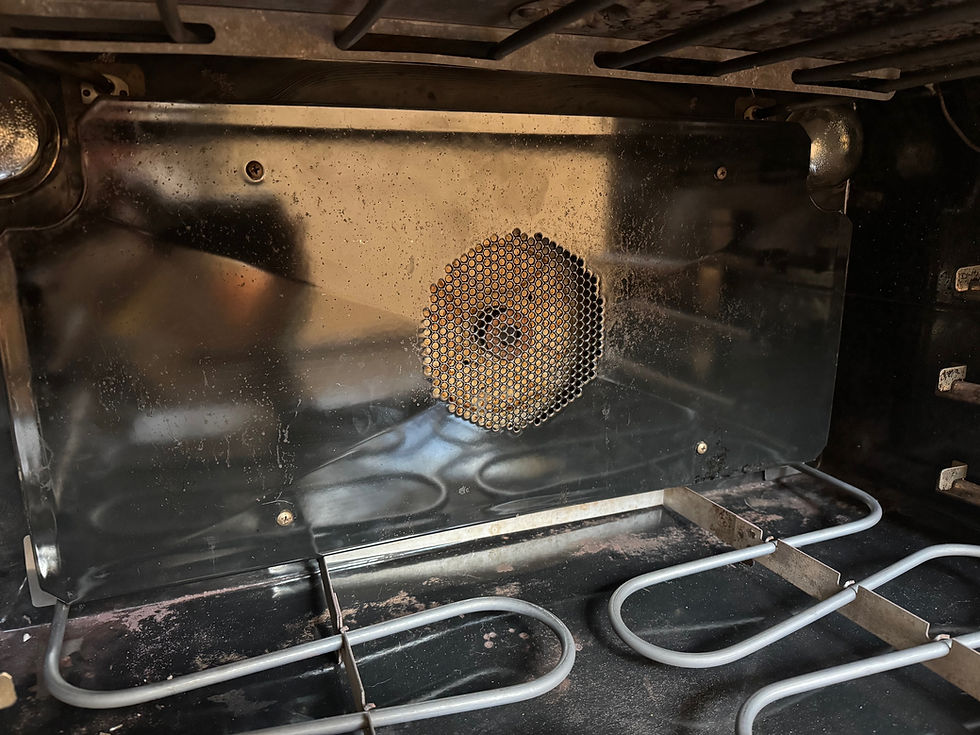
This is an "after" shot, but you can see how the screws holding in the baking coil are obstructed.

With the baffle out you can remove the 2 screws and pull the coil forwards to disconnect it. Be careful that the wires don't get lost in the rear panel. They can be tight. The cradle/frame that holds the coil has 10 metal tabs bent over it to hold it in place. (also an 'after' pic)
The coil came out with 2 screws, and then disconnecting the wire on each side. I measured the resistance expecting it to be open (no continuity) but it measured just over 11 ohms of resistance. So it seemed ok, but it could not hurt to replace after all these years, and I had already bought a new one. I was rushing to try and get the thing going before we hosted Christmas dinner. While we waited for it to arrive, Mrs P found the original paperwork for the range that the prior owners had left us. It had a schematic as well as a wiring diagram.
The new coil came, I mounted it in the cradle & I hooked it up but nothing had changed. The new coil was also around 11.5 ohms. Ok. We eliminated one thing at least.
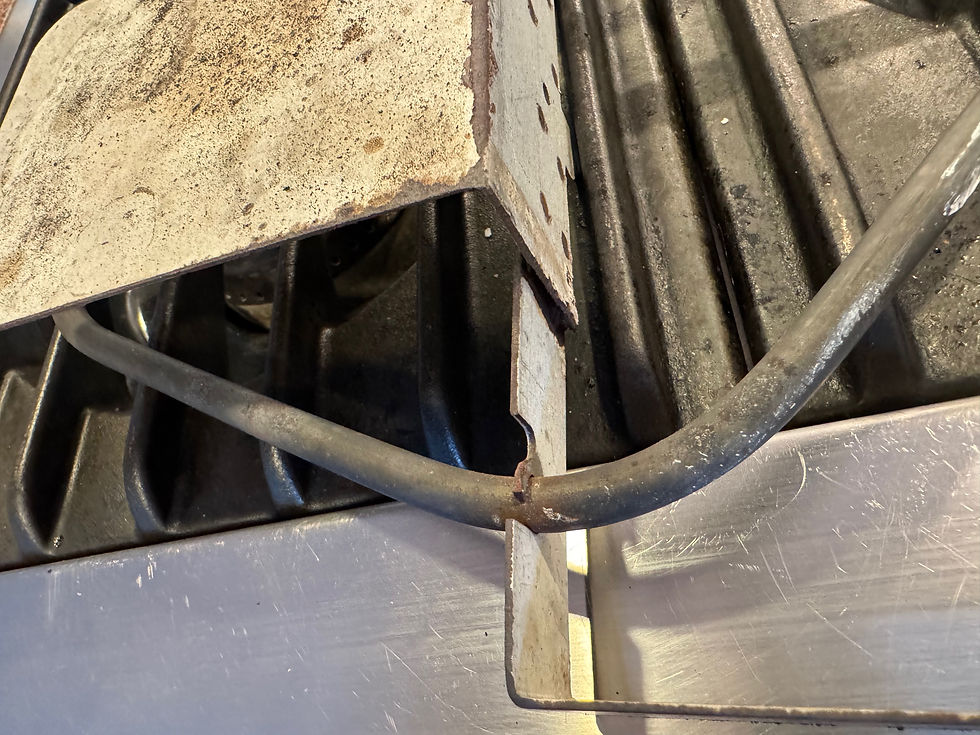
One of the 10 tabs that locates the heating coil. I used pliers to gently bend them out of the way and then bend them back over the new coil.
What this implied is that the coil was ok, so it must not be getting power. They are super simple devices - you put 240V across them and they get hot. The schematic is complicated by all of the safety switches - there is a high temp cutoff, a safety switch in the over door, the thermostat, and so on. But at the end of the day you have a button to turn it on, "bake", and you have a thermostat (to cut power to the relay when the oven gets to temp) and you have a relay to control power to the coil. The switch could be bad, but the broiler coil was turning on, as were the indicator LEDs for the oven being on and the "heating" LED, indicating it was not at temp yet. That made the switch a less likely suspect.
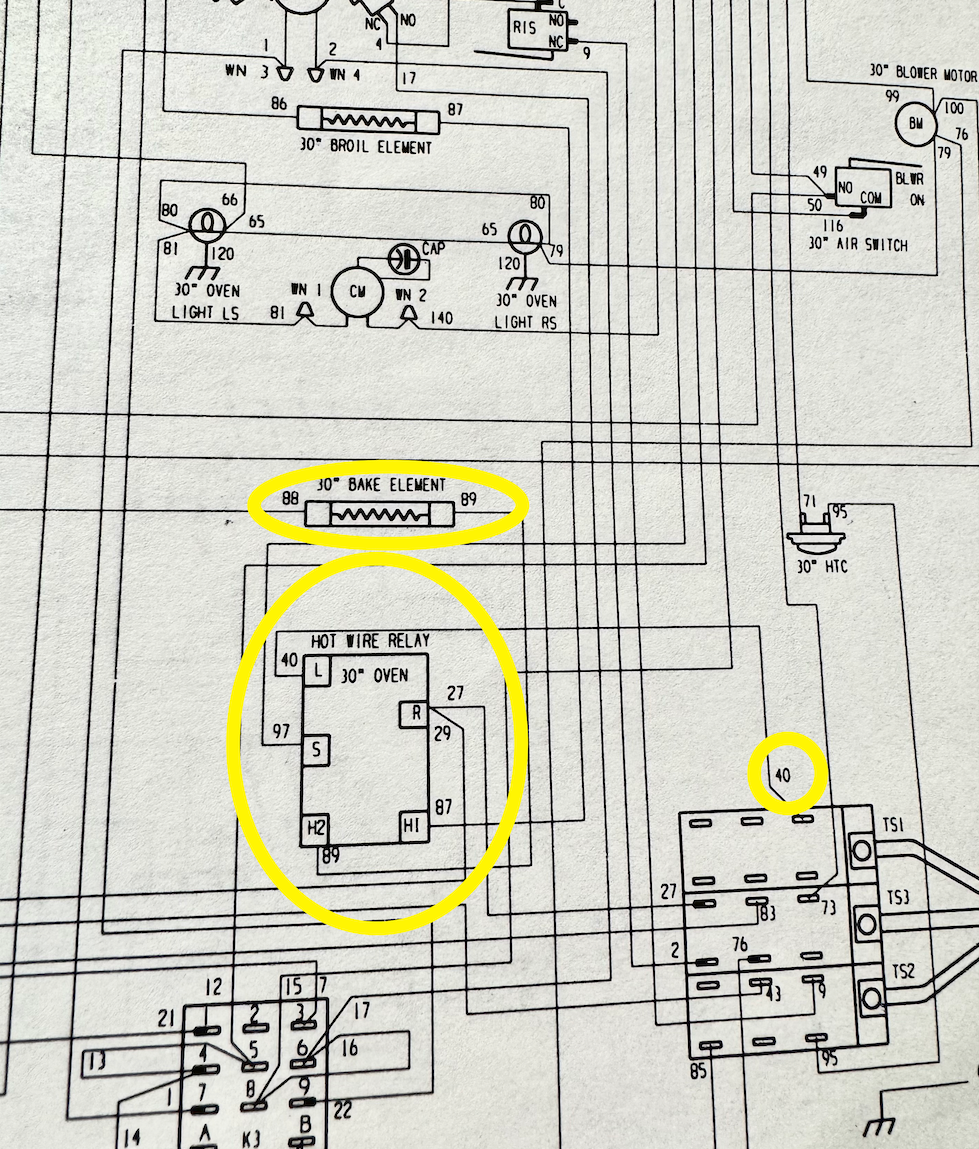
On the wiring diagram above, you can see the 240V service (LR corner) and the Hot Wire Relay (highlighted), as well as the bake element. If you follow wire 40 from the 240V terminal (T51) you can see it runs to terminal "L" on the relay. Terminal H2 runs to the bake element, terminal H1 runs to the broiler element. R & S are the two ends of the heating element that operates the relay. (complete electrical docs below)

On the schematic, the relay's coil is highlighted and terminals R & S are indicated. The dotted line runs up the the switch portion (shown below). That bottom line is one of the 240V legs, the middle line that is parallel is the Neutral which means the relay coil runs on 120V. The high temp cutout ("HTC") takes a 240V feed up to the heating elements ("BK" = Bake) so if it failed it would take out both heating elements.

The upper part of the same diagram; here you can see terminals H1 & H2 switching in the heating elements and connecting them to terminal L. Terminal L is the other 240V leg.
Why use a relay? Relays are commonly used to allow low current circuits to control high current circuits. They help make things cheaper, lighter, smaller, all those good things. Here we have to switch up to 9,000 Watts of power on and off. (around 28 Amperes of current, which is a lot)
In the oven, the coils are each pulling thousands of watts of power. The schematic had a couple of switches that were labelled "hot wire relay". I had never heard this term before so it was back to the internet for that. But first I did more basic checks: Now armed with the wiring diagram I found the hot wire relay behind a kick-panel at the bottom of the front of the stove, and then measured then voltage on the terminals that controlled the coils. Oven off, no voltage. Ok. Oven on, the broiler coil got 240V, the baking coil still had zero. That told me the relay was bad - both connect to terminal L when the relay is activated.
Hot Wire Relay Part Numbers:
DCS: 210768
GE: WB21X5362
Whirlpool: 4325190
Thermador/Bosch: 414589 or 485439
Invensys (now owned by Schneider): KS-64600-5
Frigidaire: KS 64601-1 (looks like a very close Eaton/Invensys part?) 6 terminals rather than 5.
One other number I ran into was 14-19-129 but I'm not sure which mfr it goes with.
I had to find one on ebay as they are NLA, and luckily the schematics also had part lists with part numbers I could use to search. Prices ranged from $100 to over $500. It's important to shop carefully and try all of the cross referenced brands and part numbers you can find.
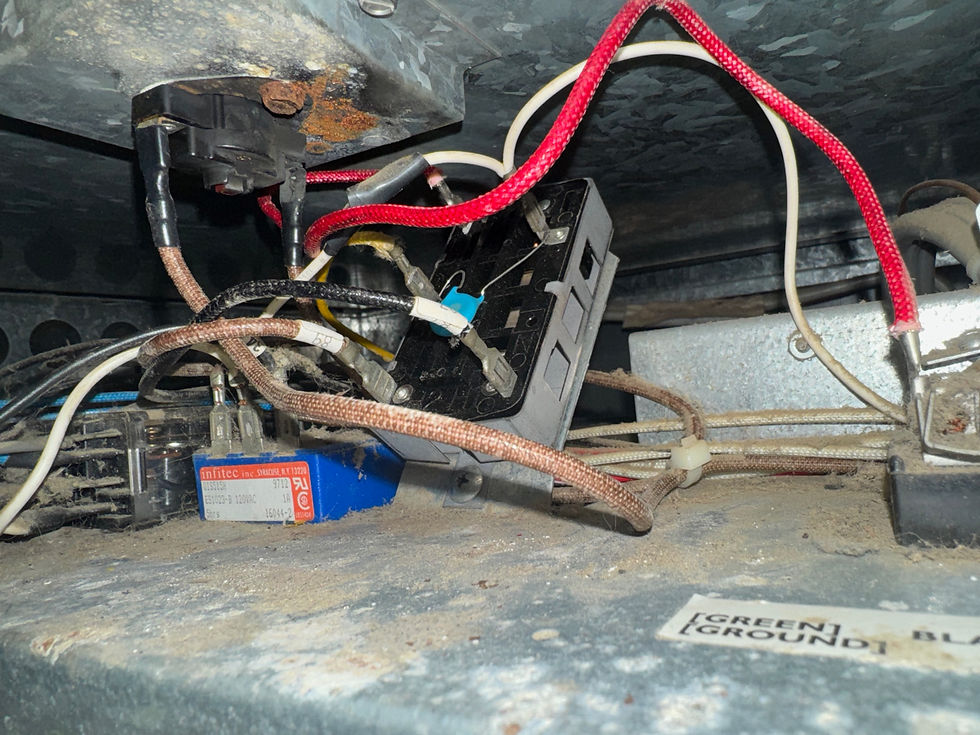
The new (used) hotwire relay mounted in the bottom of the oven. H2 & H1 terminals are the the bottom of it, and the 240V service is out of frame to the right (you can follow the red wire from L to the terminal on the RH side of the pic though). The black thing above it is the high temp cutoff switch. I clipped one meter lead to the 240V service so I would only be probing with one hand. This is basic but critical electrical safety stuff.
This hot wire relay was used by GE, DCS, Whirlpool & Thermador and was made by Eaton. One of the keys to fixing anything is to figure who made what. A lot of the more generic parts will be made by someone else. I already knew the ignitors I replaced a year ago were a Bosch part.
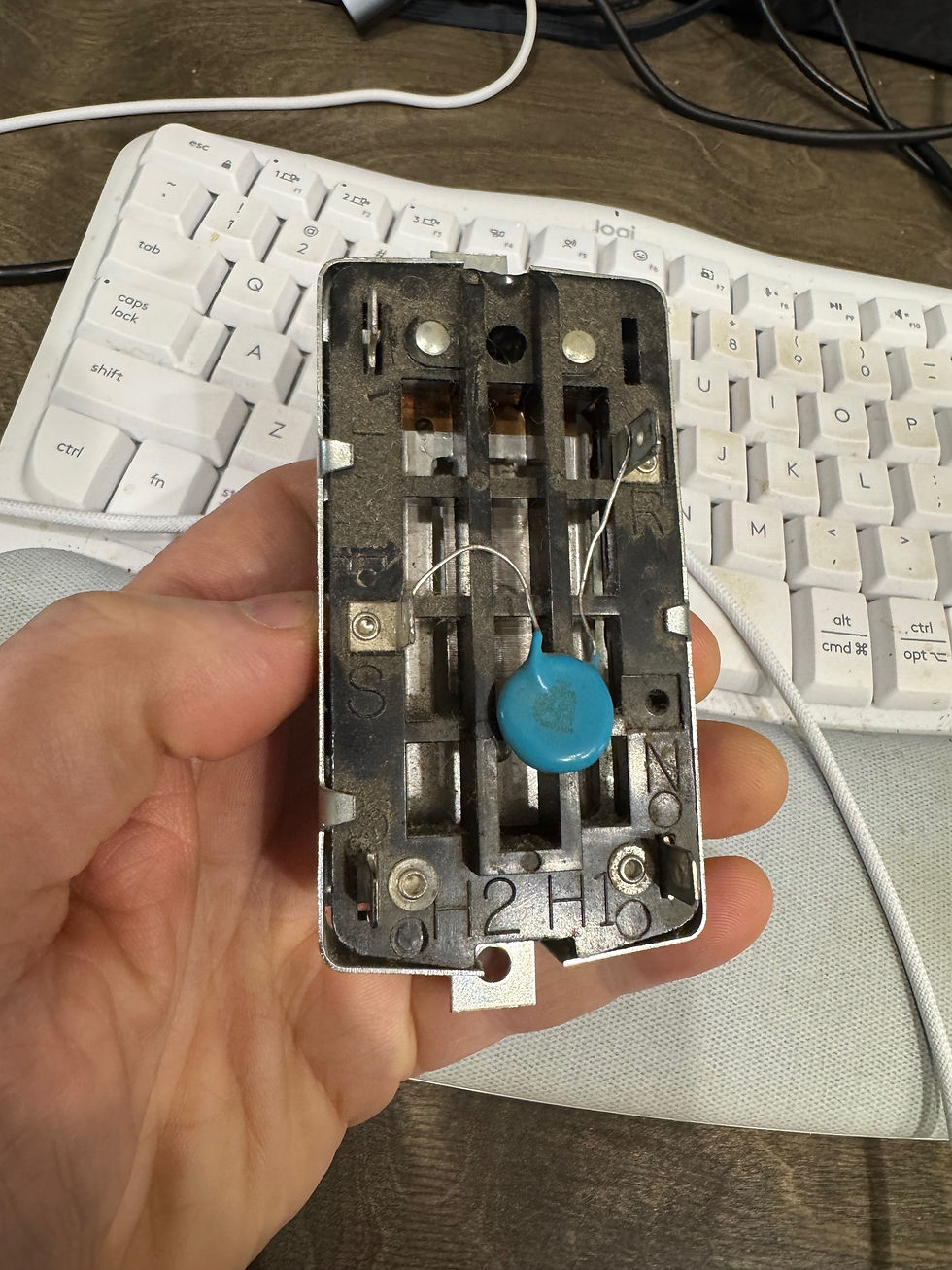
The business side of the hotwire relay. H2 is where the oven coil connects, H1 is where the broiler coil connects. This is the same orientation it has in the Oven. R & S are the "hot wire" connections, and L (upper LH corner) is the 240V feed that gets switched to H1 & H2. You can see them labelled on the block diagram and schematic (below) The Blue thing on the back (not in the schematic) is a MOV, a surge protector that is presumably there to protect the coil.
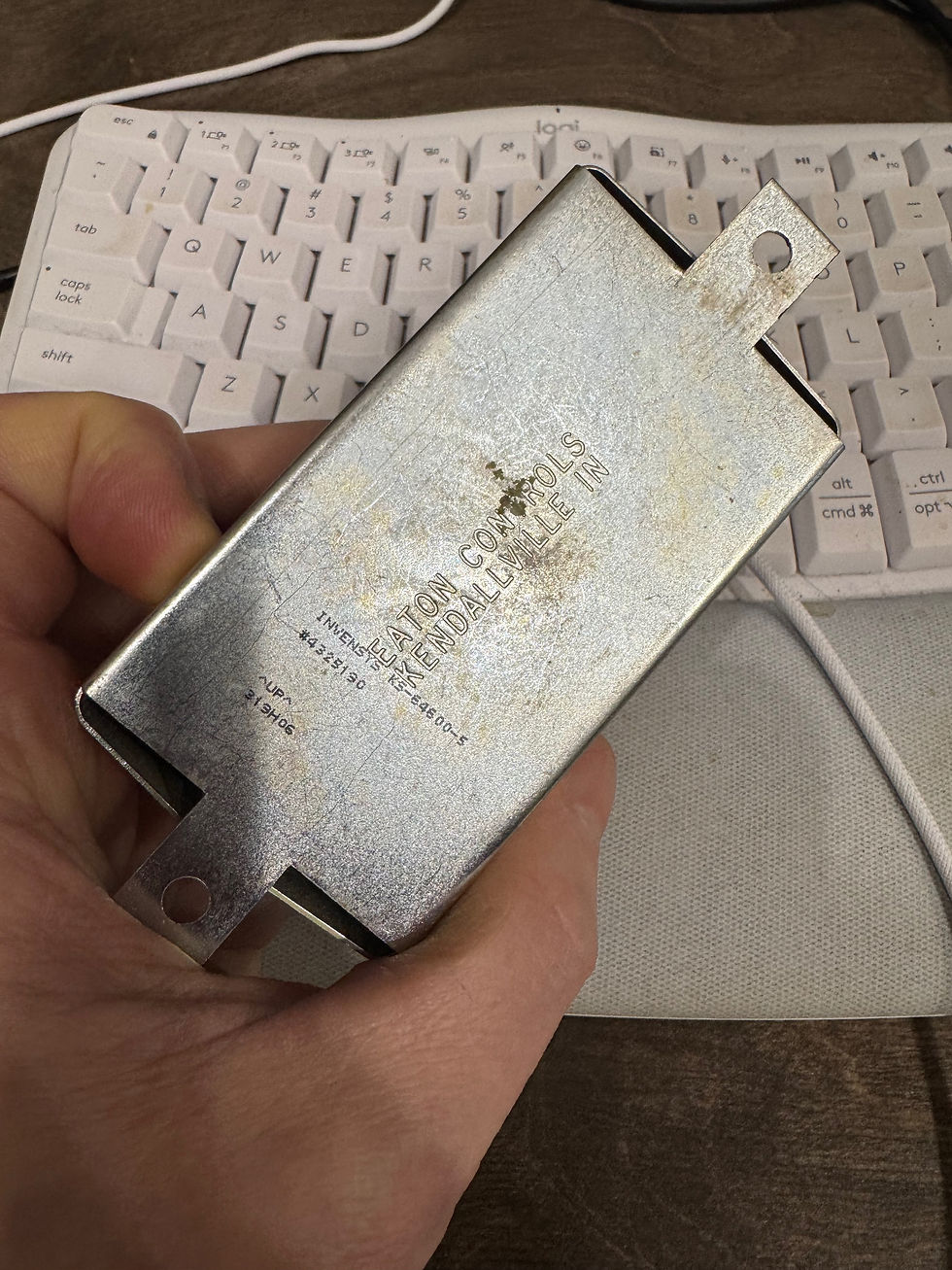
On the backside you can see the Eaton Controls part number. The DCS part number ties out to GE, Thermador and Whirlpool. It looks like the other number on the rear might tie out to Frigidaire. (?)
Fun Facts: The hot wire relay is a neat device that solves a couple of problems in the stove. Problem No.1 is the current switching (above), but problem No.2 is a bit less intuitive. In a gas oven you can turn the flame up and down and find an equilibrium point where it stays pretty close to where you want it (*for the sake of argument at least). Electric coils in contrast are big and dumb - they just get hot. The thing pulls over 11 Amperes of current at 240V and gets red hot. Your choices are usually full power hot, half power hot or off*. We get the oven to 250F or 350F or 475F by turning it on and off at intervals. So far so good? But here is the issue: if you track the oven temp too closely, the relay will be turning the oven coil on and off a lot when you reach the target temp. If you used a normal relay with a coil and some contacts you might hear persistent clicking from it as you baked, and it would probably wear out sooner since it is getting a lot of use. What to do...
(* on the schematic you can see the broiler element looks like it gets fed either 240V for broiling or cleaning, 120V for Bake or 120V via a 50% pulser for convection bake, so they can be tweaked a bit)
The "hot wire" relay uses a bimetallic strip as the contact. This is like an old style blinker in a car, or really the better analogy is the bimetallic strip used on some old fuel gauges. Think about your fuel gauge for a sec - you have gasoline sloshing around in a box and the needle does not move as it sloshes. How is that possible? The engineers add hysteresis - they average out the reactions, slow them down. In our antique VW Beetle they did this with a bimetallic strip inside the gauge. (link below) This helps prevent it from responding quickly to anything. If you drive up or down a long hill it will still give you a bad reading, but in normal driving it will be pretty stable. This is what we want for our oven - a slower response to temperature changes, and preferably a quiet one. Cool pics in that electronics exchange post btw.
I popped the new relay in and the oven coil worked again, success! Now I just had to get the thing back together. I also gave the oven a good scrub first while it was empty. The heating coil sits in a frame that has metal tabs bent around it to hold it in place. PITA. I got the new coil set into the frame, and then connected it up and screwed it into place.
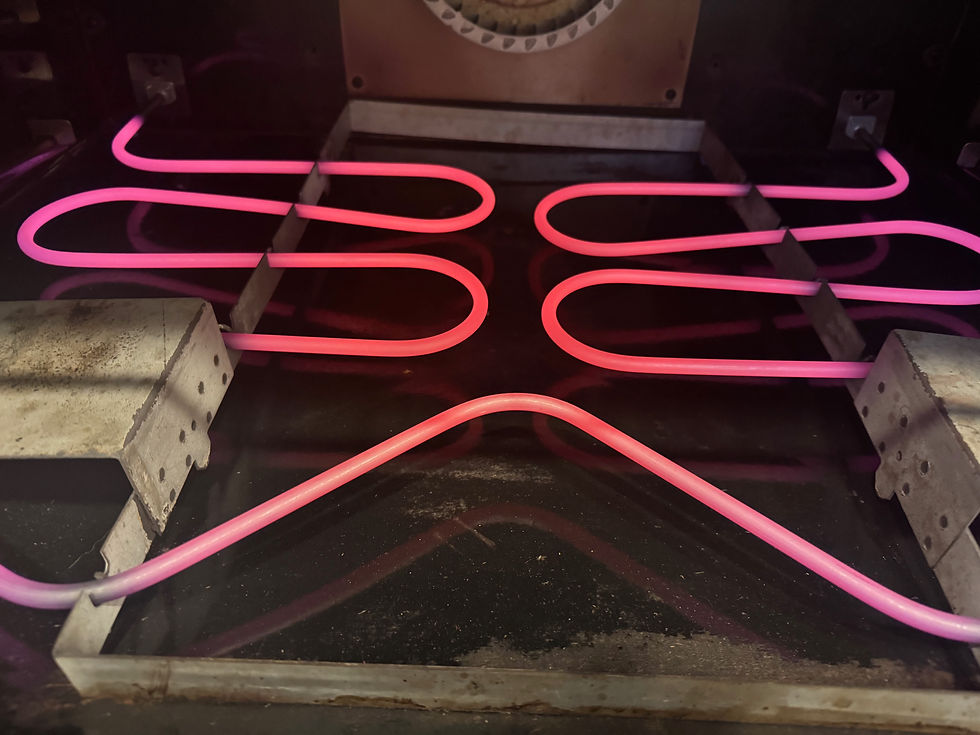
It works again!
Now to get the baffle back in. Years of dealing with oddball car issues in cramped quarters was a help here. I assembled all 4 screw/washer/spacer combos and put my screwdriver on the lower left screw - the one I can't reach behind. I wanted to get that one started (not tight though) and then use it to located the baffle so I could get the other 3 started. Once all 4 were started I could tighten it up. I had to move this into position with the panel vertical after all the parts were staged in place. I had to do all this inside an oven, with two hands, without bumping my head & without letting the other assemblies fall apart behind the baffle. It took a couple of tries, (and my head hurts) but I got it. But omg what a poor design. A couple of simple cutouts around the coil mounting screws would have made this 10X easier, and why not tack weld the spacers in place? No idea what they were thinking here. Feels like a "Friday afternoon at 5PM" kind of feature.

Each long sheet metal screw went through the baffle and then through 2 washers and a copper spacer tube. None of it was held in place by anything..
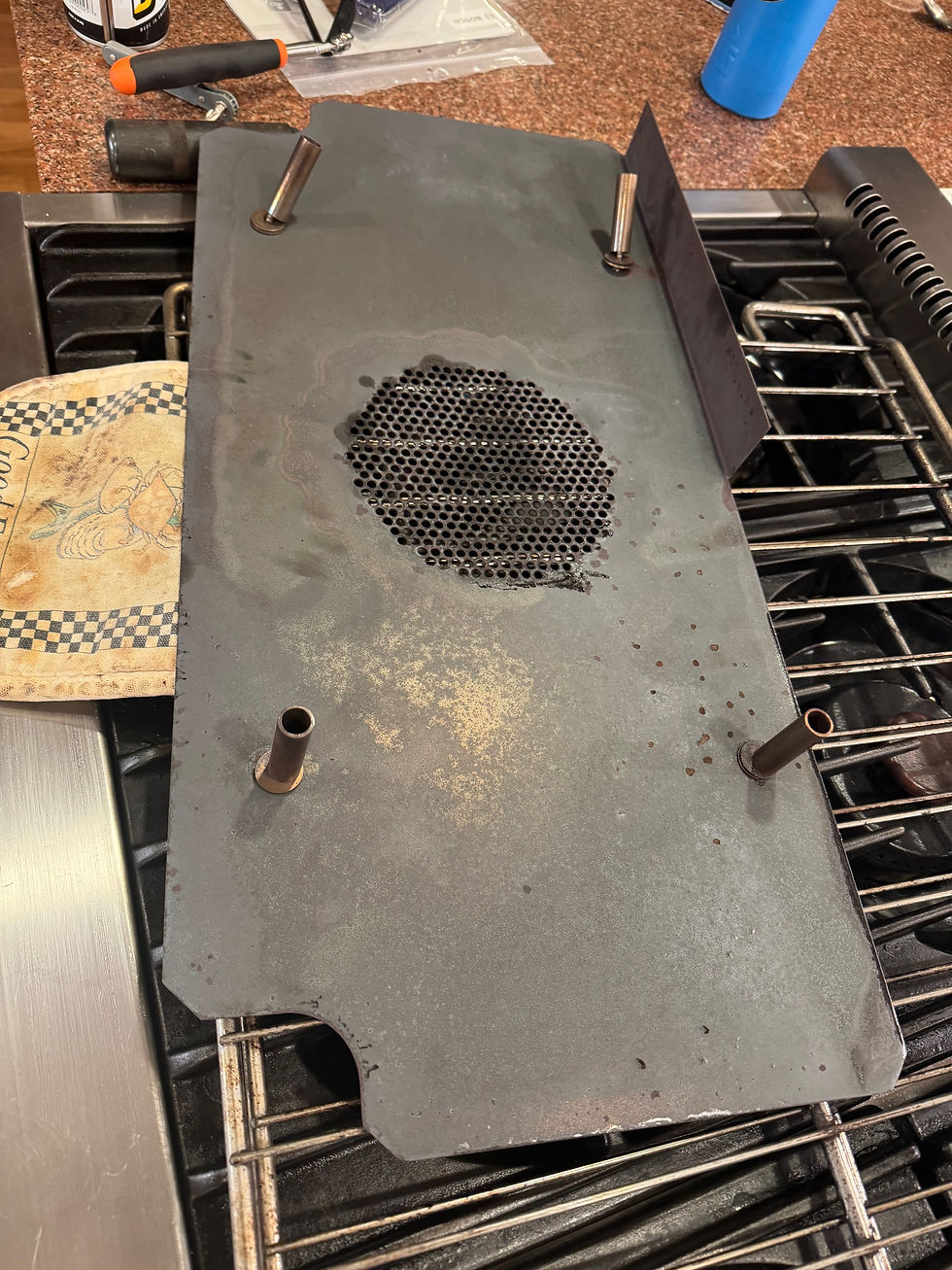
I pre-assembled all 4 in preparation for re-assembly. You can that extra bit of baffle (upper RH corner in pic) which prevents you from holding the lower LH screw assembly. Why? No idea. Up side of baffle is left here, with the cutouts for the oven lamps.
Further searches and reading indicated that I may be able to open up the old relay and just burnish the contacts to get it working again. When I attempt that I'll update this entry. It would be nice to have a spare.
I also looked for open source oven fixing projects, hoping to find some generic control circuits or something, but have not found one that would have helped here. There are replacement circuit boards for some common models you can buy. But those are all newer digitally controlled units. (anyone?)
The fundamental issue for me is that this is just a fancy stainless steel box with some basic electric widgets inside. Replacing it can easily cost 4 or 5 figures, and there is really nothing wrong with the "box"; it's going to be a widget or some cheap burner part that rusted. Tossing it into a landfill certainly seems both expensive and very wasteful. Despite my whining about the convection baffle, we do really like the range. I spent a bit under $500 on parts & shipping to get this fixed, so by comparison I saved thousands. If I had more experience (and time!) going in I would not have bought the extra heating coil and would have fixed this for even less. I was in a rush and I took a calculated risk. Worst case is I have a nice new heating element that should go another 20+ years.
I am tempted to buy a thermostat and maybe a switch just in case though.
References:
Electronics Exchange: https://electronics.stackexchange.com/questions/630939/can-i-replace-this-thermal-relay-with-a-conventional-electromechanical-relay
Lets Talk Parts (Sells DCS parts, and where I got the baking element) https://www.letstalkparts.com/
How Old VW Fuel Gauges work: https://www.nls.net/mp/volks/htm/fuel_ga.htm
Invensys is Schneider: https://www.se.com/us/en/brands/invensys/invensys.jsp
Eaton Corp: https://en.wikipedia.org/wiki/Eaton_Corporation
Hysteresis: https://en.wikipedia.org/wiki/Hysteresis#
Electric Info For Stove:
Parts List & diagrams (Not 100% exact but very close)
Comments